What’s Next for Smart Factories?
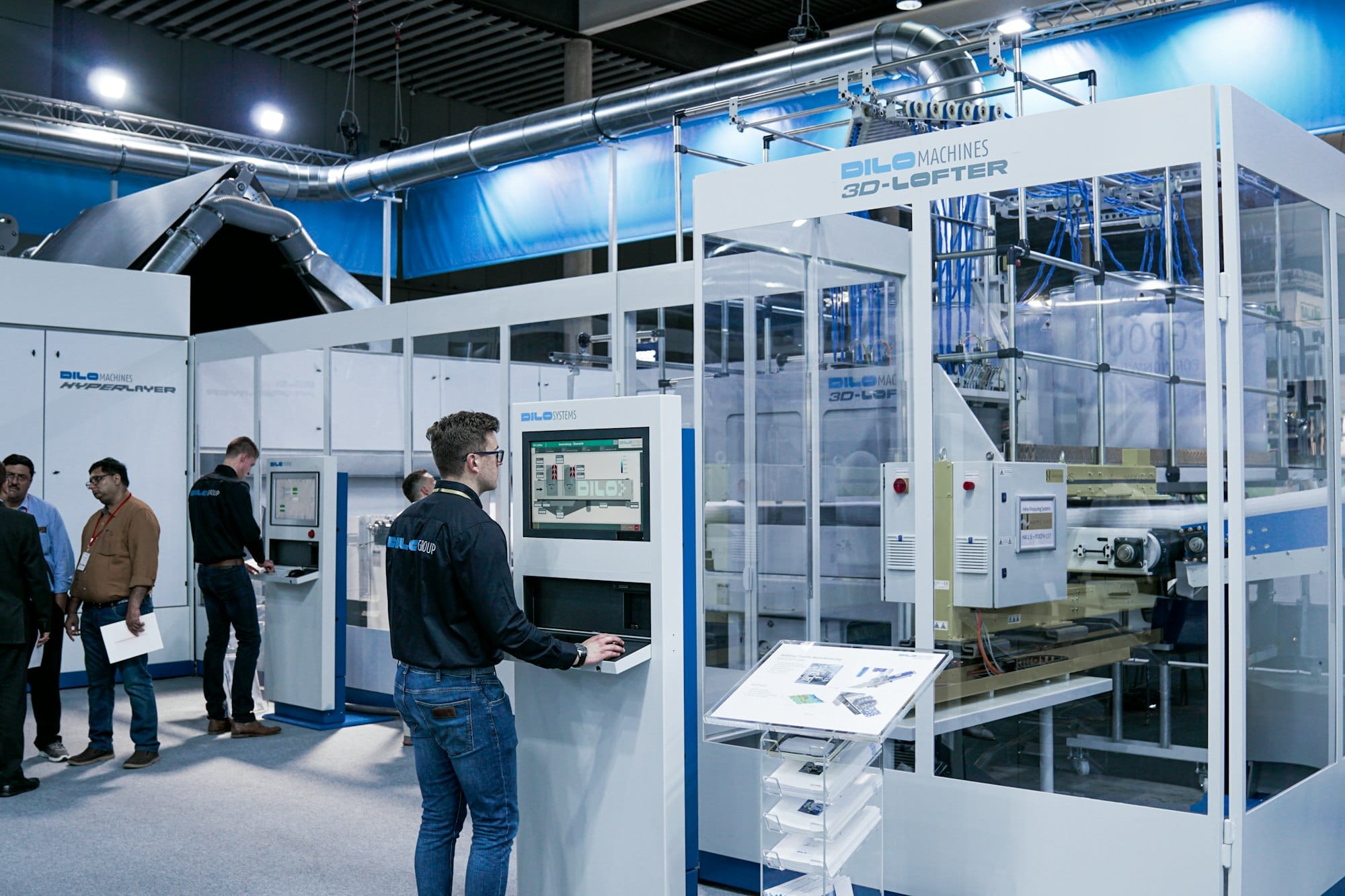
The manufacturing industry is undergoing a seismic transformation, driven by the rapid adoption of advanced technologies that redefine how factories operate. Smart factories, the cornerstone of Industry 4.0, are evolving into dynamic, interconnected ecosystems where artificial intelligence (AI), the Internet of Things (IoT), robotics, and data analytics converge to optimize efficiency, enhance productivity, and ensure sustainability. As we move into 2025, the integration of these technologies is accelerating, paving the way for unprecedented innovation and operational excellence.
At the heart of this evolution is the growing role of Generative AI, which is unlocking new value for manufacturers by analyzing vast amounts of data collected from IoT devices and machines on the factory floor. These AI-driven tools are enabling manufacturers to identify inefficiencies, recommend actionable insights, and improve processes in real-time, as highlighted in CDA's Smart Factory Predictions for 2025. This shift marks a departure from isolated pilot projects to scalable, mainstream applications of AI across factories of all sizes.
Another critical trend is the rise of Digital Twins, which create virtual replicas of physical assets, processes, or systems. These digital models allow manufacturers to simulate, monitor, and optimize operations with unparalleled precision. As noted in Advances in Computational Intelligence, Digital Twins are proving invaluable in reducing costs, minimizing waste, and enhancing product quality, while also preparing the industry for the human-machine collaboration emphasized in Industry 5.0.
Furthermore, the increasing adoption of cloud computing and edge computing is enabling real-time data processing and seamless connectivity across manufacturing systems. These technologies are empowering manufacturers to make data-driven decisions, improve supply chain visibility, and enhance resource allocation, as explored in the 2025 Smart Factory Report by StartUs Insights.
Sustainability is also emerging as a key focus area, with manufacturers leveraging technologies to monitor and reduce their carbon footprint. From energy-efficient systems to eco-friendly practices, the push for sustainable manufacturing aligns with global efforts to combat climate change, as discussed in Priority Software's Smart Manufacturing Trends 2025.
As these technologies converge, they are not only reshaping factory operations but also addressing critical challenges such as labor shortages, supply chain disruptions, and cybersecurity risks. The journey toward smarter, more resilient factories is well underway, and the next wave of innovation promises to redefine the future of manufacturing.
Generative AI for Process Optimization
Generative AI is revolutionizing smart factories by enabling manufacturers to analyze vast amounts of data and automate decision-making processes. Unlike traditional AI models, generative AI can create new data, scenarios, or solutions based on learned patterns, making it a powerful tool for predictive maintenance, quality control, and production planning.
For instance, manufacturers can use generative AI to simulate production line adjustments and predict their impact on efficiency, reducing downtime and waste.
Generative AI also enhances the ability to identify bottlenecks in real-time by analyzing data from IoT sensors and machine logs.
According to CDA, this technology is expected to become mainstream in 2025, with applications ranging from predictive maintenance to automated quality assurance. The integration of generative AI into manufacturing processes could unlock billions in value by reducing operational inefficiencies and enabling rapid prototyping without physical trials.
Edge Computing for Real-Time Decision Making
Edge computing is emerging as a critical enabler for smart factories by addressing the latency and bandwidth challenges associated with cloud computing. By processing data locally at the edge of the network, factories can achieve real-time decision-making capabilities, which are essential for applications like robotics, autonomous systems, and quality control.
Unlike cloud computing, edge computing reduces the need to transmit large volumes of data to centralized servers, minimizing delays and ensuring faster response times. This is particularly beneficial for time-sensitive operations, such as monitoring machine performance or detecting defects during production.
As noted in the StartUs Insights report, edge computing also enhances cybersecurity by keeping sensitive data within the factory's local network, reducing exposure to external threats.
Additionally, edge computing supports the integration of advanced technologies like augmented reality (AR) for maintenance and training purposes. By processing AR data locally, workers can receive real-time guidance and diagnostics, improving productivity and reducing errors.
Digital Twin Technology for Predictive Analytics
Digital twin technology, which creates virtual replicas of physical systems, is transforming how factories monitor, simulate, and optimize their operations. By integrating real-time data from IoT sensors, digital twins provide manufacturers with a comprehensive view of their production processes, enabling them to predict equipment failures, optimize workflows, and test new strategies without disrupting actual operations.
For example, a factory using digital twin technology can simulate the impact of introducing a new production line or altering supply chain logistics. This allows for proactive decision-making and reduces the risk of costly errors.
According to AIUT, digital twins are becoming indispensable tools for achieving full industrial digitalization and aligning with Industry 4.0 objectives.
Moreover, digital twins are increasingly being used to enhance sustainability efforts. By simulating energy consumption and waste generation, manufacturers can identify opportunities to reduce their environmental footprint. This aligns with the growing emphasis on sustainable manufacturing practices, as highlighted in the Smart Machines & Factories report.
Blockchain for Supply Chain Transparency
Blockchain technology is gaining traction in smart factories for its ability to enhance supply chain transparency and security. By creating an immutable ledger of transactions, blockchain enables manufacturers to track the origin, movement, and authenticity of raw materials and finished goods. This is particularly valuable in industries like pharmaceuticals and electronics, where traceability is critical for regulatory compliance and consumer trust.
The integration of blockchain with IoT devices further amplifies its impact by enabling real-time tracking and verification of goods.
For example, sensors embedded in shipments can record temperature, humidity, and location data, which is then stored on a blockchain to ensure the integrity of perishable goods.
According to Life Conceptual, the blockchain supply chain market is projected to grow at a compound annual growth rate (CAGR) of 67.3%, reaching $3.4 billion by 2025.
Blockchain also supports ethical manufacturing practices by providing verifiable data on labor conditions and environmental compliance. This is increasingly important as consumers and regulators demand greater accountability from manufacturers.
Collaborative Robotics for Flexible Automation
Collaborative robots, or cobots, are redefining automation in smart factories by working alongside human operators to perform tasks that require precision, flexibility, and adaptability. Unlike traditional industrial robots, cobots are designed to be safe for human interaction, with features like force-limiting sensors and advanced motion control.
Cobots are particularly effective in tasks that require a combination of human dexterity and robotic consistency, such as assembly, quality inspection, and material handling. Their ability to adapt to changing production requirements makes them ideal for small-batch manufacturing and customized production runs.
The adoption of cobots is also addressing the labor shortage in the manufacturing sector. By automating repetitive and physically demanding tasks, cobots free up human workers to focus on higher-value activities, such as process optimization and innovation.
According to AIUT, the integration of collaborative robotics with mobile platforms is creating mobile production stations that can perform tasks across different areas of the factory, further enhancing flexibility and efficiency.
In addition to their operational benefits, cobots are cost-effective, with lower upfront investment and faster deployment compared to traditional automation systems. This makes them accessible to small and medium-sized enterprises, democratizing the benefits of automation.
By leveraging these transformative technologies, smart factories are poised to achieve unprecedented levels of efficiency, flexibility, and sustainability. As manufacturers continue to navigate the challenges of a dynamic global market, the adoption of generative AI, edge computing, digital twins, blockchain, and collaborative robotics will play a pivotal role in shaping the future of manufacturing. These innovations not only enhance operational performance but also position factories to meet the evolving demands of customers, regulators, and stakeholders.
AI-Driven Quality Assurance and Control
Artificial Intelligence (AI) is transforming quality assurance (QA) and quality control (QC) processes in manufacturing by enhancing precision, speed, and scalability. Unlike traditional QA/QC methods, which rely heavily on manual inspections and static sampling, AI-powered systems utilize machine learning (ML) and computer vision to perform real-time inspections across entire production lines. These systems can identify defects, deviations, and inconsistencies at a granular level, ensuring higher product quality while minimizing waste.
For example, AI-driven computer vision systems can analyze high-resolution images of products at speeds unattainable by human inspectors. By detecting microscopic defects or anomalies, these systems reduce the likelihood of defective products reaching consumers.
According to Quality Magazine, manufacturers leveraging AI in QA/QC have reported up to a 30% improvement in defect detection rates, leading to significant cost savings and enhanced customer satisfaction.
Additionally, AI systems can rationalize the number of QA/QC tests conducted by analyzing historical data and identifying critical control points. This not only reduces testing costs but also accelerates production timelines. By integrating AI into QA/QC processes, manufacturers can achieve a balance between efficiency and quality, a critical factor in highly competitive markets.
AI-Powered Predictive Maintenance
While predictive maintenance has been a cornerstone of Industry 4.0, AI is taking it to the next level by enabling real-time monitoring and predictive analytics. Traditional maintenance models, such as reactive or scheduled maintenance, often result in unplanned downtime or unnecessary interventions. In contrast, AI-powered predictive maintenance uses sensor data, machine learning, and Industrial Internet of Things (IIoT) technologies to anticipate equipment failures before they occur.
For instance, AI algorithms can analyze vibration patterns, temperature fluctuations, and other operational parameters to detect early signs of wear and tear.
As highlighted by OxMaint, predictive maintenance powered by AI has been shown to reduce downtime by up to 50% and extend equipment lifespan by 20-40%. This not only lowers maintenance costs but also ensures seamless operational workflows.
Moreover, AI-driven predictive maintenance solutions are becoming increasingly sophisticated, with the ability to tailor algorithms to specific equipment and operating conditions. This customization enhances the accuracy of failure predictions, allowing manufacturers to optimize maintenance schedules and resource allocation. As a result, companies adopting these technologies gain a competitive edge by minimizing disruptions and maximizing productivity.
Intelligent Workforce Management
AI is revolutionizing labor management in manufacturing by optimizing workforce allocation, improving employee training, and enhancing workplace safety.
By analyzing production demands, employee availability, and historical performance data, AI systems can create efficient work schedules tailored to meet business needs. This ensures that the right resources are allocated at the right time, reducing inefficiencies and improving shop floor productivity.
Additionally, AI identifies skill gaps among employees and recommends targeted training programs to upskill the workforce. For example, manufacturers can use AI to design personalized training modules for quality and compliance, ensuring that employees are equipped to handle complex tasks. According to Quality Magazine, this approach not only improves employee capabilities but also boosts job satisfaction and retention rates.
AI also plays a critical role in enhancing workplace safety by automating high-risk tasks and monitoring environmental conditions. For instance, AI-powered systems can detect hazardous conditions, such as gas leaks or overheating equipment, and issue real-time alerts to prevent accidents. By creating a safer work environment, manufacturers can reduce workplace injuries and associated costs, further reinforcing the value of AI in labor management.
Supply Chain Optimization with AI
AI is reshaping supply chain management by providing real-time visibility, predictive analytics, and intelligent decision-making capabilities. Traditional supply chain models often suffer from inefficiencies caused by fragmented data, manual processes, and limited forecasting accuracy. AI addresses these challenges by integrating data from multiple sources, including IoT devices, ERP systems, and external market data, to create a unified and transparent supply chain ecosystem.
One of the key applications of AI in supply chain management is demand forecasting. By analyzing historical sales data, market trends, and external factors such as weather or geopolitical events, AI algorithms can predict demand fluctuations with high accuracy. This enables manufacturers to optimize inventory levels, reduce stockouts, and minimize excess inventory costs.
According to a report by Forbes, companies leveraging AI for demand forecasting have achieved up to a 20% reduction in inventory carrying costs.
AI also enhances supply chain resilience by identifying potential disruptions and recommending mitigation strategies. For example, AI systems can analyze supplier performance data and geopolitical risks to identify vulnerabilities in the supply chain. This enables manufacturers to proactively address issues, such as sourcing alternative suppliers or rerouting shipments, ensuring continuity in operations.
Furthermore, AI-powered supply chain platforms facilitate real-time collaboration among stakeholders, enabling faster decision-making and improved coordination. By leveraging AI for supply chain optimization, manufacturers can achieve greater efficiency, agility, and resilience in an increasingly complex global market.
AI-Enhanced Product Design and Prototyping
AI is transforming product design and prototyping by enabling faster iterations, improved accuracy, and reduced costs. Traditional design processes often require multiple physical prototypes and extensive testing, which can be time-consuming and expensive. AI addresses these challenges by leveraging generative design algorithms and digital twin technology to create virtual prototypes and simulate performance under various conditions.
Generative design, a subset of AI, uses algorithms to explore a wide range of design possibilities based on predefined parameters, such as material properties, weight, and cost. This allows engineers to identify optimal designs more quickly and efficiently. For instance, manufacturers can use AI to design lightweight yet durable components for automotive or aerospace applications, reducing material costs and improving performance.
Digital twins, virtual replicas of physical systems, further enhance the prototyping process by enabling real-time simulations and data-driven decision-making. As noted by SotaTek, digital twins allow manufacturers to test different design iterations, identify potential flaws, and optimize production processes before building physical prototypes. This not only accelerates the design cycle but also minimizes costs associated with rework and material waste.
By integrating AI into product design and prototyping, manufacturers can bring innovative products to market faster while maintaining high standards of quality and cost-efficiency. This capability is particularly valuable in industries with rapidly evolving customer demands and competitive pressures.
AI for Energy Efficiency and Sustainability
As sustainability becomes a critical priority for manufacturers, AI is playing a pivotal role in optimizing energy consumption and reducing carbon emissions. Traditional energy management systems often rely on static models and manual interventions, which can lead to inefficiencies and higher costs. AI, on the other hand, uses real-time data and predictive analytics to optimize energy usage across manufacturing facilities.
For example, AI algorithms can analyze energy consumption patterns, production schedules, and external factors such as weather conditions to recommend energy-saving measures. This may include adjusting equipment settings, scheduling energy-intensive operations during off-peak hours, or integrating renewable energy sources. According to Manufacturing Dive, manufacturers adopting AI for energy management have reported up to a 15% reduction in energy costs and a significant decrease in carbon footprint.
AI also supports sustainability initiatives by enabling circular manufacturing practices. By analyzing product lifecycle data, AI systems can identify opportunities for recycling, remanufacturing, or repurposing materials, reducing waste and conserving resources. Furthermore, AI-powered carbon monitoring tools provide manufacturers with actionable insights to meet regulatory requirements and achieve sustainability goals.
By leveraging AI for energy efficiency and sustainability, manufacturers can not only reduce operational costs but also enhance their reputation as environmentally responsible organizations. This is increasingly important in a market where consumers and stakeholders prioritize sustainable practices.
Advanced Energy Management Systems
Smart factories are leveraging advanced energy management systems to enhance both sustainability and efficiency. Unlike traditional systems that rely on static models, these advanced systems integrate real-time data from IoT sensors, AI algorithms, and predictive analytics to optimize energy usage dynamically. For instance, IoT-enabled sensors monitor energy consumption across all equipment, while AI algorithms analyze this data to identify inefficiencies and recommend actionable improvements.
One example is the implementation of demand-response strategies, where energy-intensive operations are scheduled during off-peak hours to reduce costs and balance grid loads. Additionally, these systems facilitate the integration of renewable energy sources, such as solar and wind, into manufacturing processes.
According to a report by McKinsey, manufacturers adopting smart energy management systems have reported energy savings of up to 20%, alongside a significant reduction in greenhouse gas emissions.
This section differs from the previously covered topic of "AI for Energy Efficiency and Sustainability" by focusing on the integration of IoT and predictive analytics in energy management systems, rather than solely on AI-driven solutions.
Circular Manufacturing Practices
Circular manufacturing is becoming a cornerstone of sustainable smart factory operations. This approach emphasizes resource efficiency by designing products and processes that enable recycling, remanufacturing, and reusability. Smart factories utilize real-time data and automation to track material flows, ensuring minimal waste and maximum resource utilization.
For example, IoT sensors embedded in production lines can identify waste generation points, while AI-powered analytics suggest process optimizations to reduce material loss. Additionally, robotics and automation streamline disassembly processes, facilitating the recovery of valuable materials for reuse.
A study by the Ellen MacArthur Foundation highlights that adopting circular manufacturing practices can reduce raw material costs by up to 30% and cut waste generation by 50%.
While the existing content on circular manufacturing focuses on its role in the circular economy, this section delves deeper into how smart factories operationalize these practices through IoT, AI, and robotics.
Real-Time Environmental Monitoring
Smart factories are increasingly deploying real-time environmental monitoring systems to track and mitigate their ecological impact. These systems utilize IoT sensors and cloud-based platforms to provide continuous data on emissions, energy usage, and waste generation. For example, sensors can measure air quality and detect harmful emissions, while cloud platforms aggregate this data for analysis and reporting.
By integrating these systems with AI, manufacturers can predict environmental risks and take proactive measures to address them. For instance, AI algorithms can forecast potential regulatory violations based on historical data and recommend adjustments to production processes.
According to Deloitte Insights, companies using real-time environmental monitoring have achieved compliance rates of over 95% with environmental regulations, while also reducing their carbon footprint.
This section expands on the concept of sustainability by focusing on real-time monitoring and predictive analytics, which were not covered in the existing content.
Workforce Empowerment for Sustainable Operations
Human capital plays a critical role in achieving sustainability and efficiency in smart factories. Advanced training programs are equipping workers with the skills needed to operate and maintain smart manufacturing technologies. For example, augmented reality (AR) tools are being used to provide hands-on training for complex tasks, such as equipment maintenance and energy optimization.
Moreover, collaborative platforms enable cross-functional teams to work together on sustainability initiatives. These platforms integrate data from various sources, allowing teams to identify inefficiencies and develop solutions collaboratively.
A report by PwC found that companies investing in workforce empowerment for sustainability saw a 15% increase in operational efficiency and a 20% reduction in resource consumption.
This section differs from existing content by emphasizing the role of human capital and collaborative tools in driving sustainability, rather than focusing solely on technological solutions.
Data-Driven Decision Making for Resource Optimization
Data analytics is at the heart of resource optimization in smart factories. By collecting and analyzing vast amounts of data from IoT devices, manufacturers can gain actionable insights into their operations. For instance, advanced analytics can identify underutilized equipment, enabling manufacturers to optimize production schedules and reduce energy waste.
Additionally, machine learning algorithms can predict resource demand based on historical trends and external factors, such as market conditions and supply chain disruptions. This allows manufacturers to adjust their operations in real time, minimizing resource wastage and ensuring supply chain resilience.
According to a study by BCG, data-driven resource optimization can reduce operational costs by up to 25% while enhancing overall efficiency.
This section builds on the concept of data analytics but focuses specifically on its application for resource optimization, which has not been addressed in existing content.
By exploring these distinct aspects of sustainability and efficiency in smart factory operations, this report provides a comprehensive view of how advanced technologies and practices are reshaping manufacturing for a more sustainable future.
Conclusion
The research highlights how transformative technologies are reshaping smart factories, driving unprecedented levels of efficiency, flexibility, and sustainability. Key advancements include generative AI, which optimizes production processes through predictive maintenance and rapid prototyping, and edge computing, which enables real-time decision-making while reducing latency and enhancing cybersecurity. Digital twin technology is revolutionizing predictive analytics by simulating operations and optimizing workflows, while blockchain ensures supply chain transparency and security.
Additionally, collaborative robotics (cobots) are redefining automation by working alongside human operators to enhance flexibility and address labor shortages. These technologies collectively position manufacturers to meet the demands of a dynamic global market while reducing costs and environmental impact.
The implications of these advancements are profound. Technologies like AI-driven predictive maintenance and digital twins are enabling proactive decision-making, reducing downtime, and improving resource utilization. Meanwhile, blockchain and circular manufacturing practices are fostering ethical and sustainable operations, aligning with growing consumer and regulatory demands for accountability.
The integration of AI-powered energy management systems and real-time environmental monitoring is further driving sustainability by reducing energy consumption and emissions. As these technologies mature, manufacturers must prioritize workforce empowerment through advanced training and collaborative platforms to fully realize the potential of smart factories.
Looking ahead, the adoption of these innovations will be critical for achieving Industry 4.0 objectives and maintaining competitiveness in an increasingly complex manufacturing landscape. Manufacturers should focus on scaling these technologies, fostering cross-functional collaboration, and aligning their operations with sustainability goals to unlock long-term value.